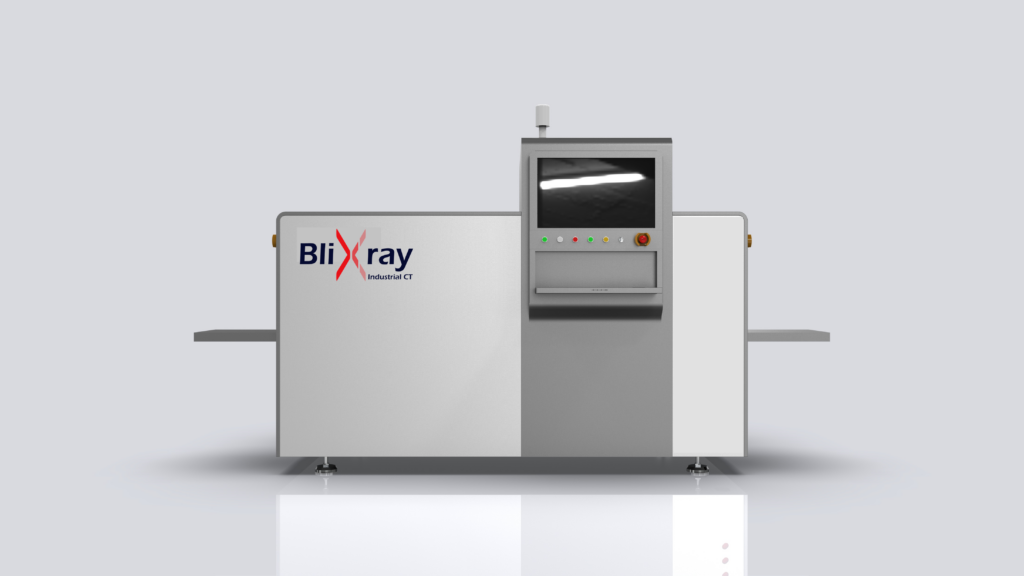
In the rapidly evolving landscape of electric vehicle (EV) manufacturing, ensuring the quality and safety of lithium-ion battery cells is paramount. A critical aspect of this quality control is the precise measurement of anode overhang, which plays a crucial role battery safety and quality. Traditional inspection methods have struggled to keep pace with the demands of high-volume production while maintaining the necessary accuracy and reliability.
This presentation introduces a groundbreaking inline CT solution that has transformed the quality inspection process for battery electrode overhang. Our system performs full 3D scans of all four corners of each battery cell, while achieving an unprecedented throughput of 40 cells per minute. This remarkable speed represents a significant leap forward in inline inspection capabilities, enabling manufacturers to implement 100% inspection without compromising production efficiency.
The core of our innovation lies in the seamless integration of cutting-edge Ganty CT hardware and proprietary Analysis Algorithms. This combination allows for rapid battery positioning, image acquisition and processing of detailed 3D data, providing accurate measurements of anode overhang dimensions and detecting subtle defects that might otherwise go unnoticed.
Key features of our solution include:
1. Real-time 3D visualization of battery cell structure
2. Automated measurement and analysis of anode overhang
3. AI-driven defect detection for improved accuracy and consistency
4. Seamless integration with existing production lines
5. Comprehensive data logging for traceability and process optimization
The implementation of this technology offers numerous benefits to battery manufacturers, including increased production yield, reduced scrap rates, and enhanced overall product quality. By enabling early detection of manufacturing issues, our system allows for rapid adjustments to production parameters, minimizing costly defects and potential safety risks.
This presentation will delve into the technical aspects of our inline CT solution, discussing the challenges overcome in achieving high-throughput 3D scanning and analysis. We will present case studies demonstrating the system’s performance in real-world manufacturing environments, highlighting its impact on production efficiency and product quality.
Furthermore, we will explore how this technology aligns with industry standards and contributes to the ongoing efforts in measurement traceability and standardization within the EV battery manufacturing sector. The versatility of our solution extends beyond battery inspection, with potential applications in other high-precision manufacturing domains such as aerospace, additive manufacturing, and medical device production. Join us to discover how this innovative approach is setting new benchmarks in quality control for the EV industry and beyond.